ライニング
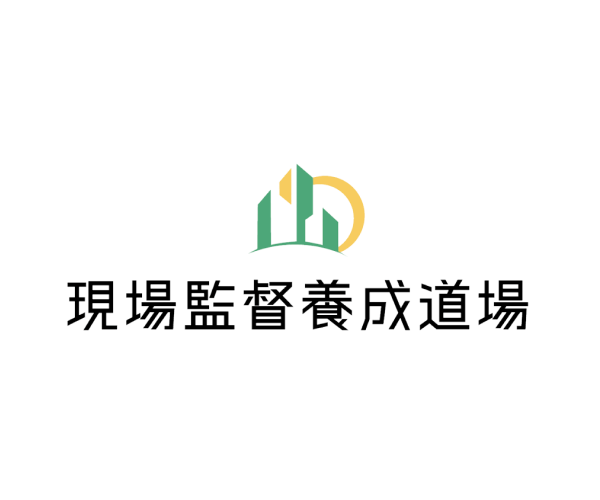
ライニングとは、物体の表面や内部に施される表面処理を指します。
この処理は、対象物の摩耗、耐食性、耐酸性、耐熱性などを向上させることを目的としています。
特に、ライニングは複数のコーティング層によって構成され、これによって耐久性を向上させます。
ライニング処理された表面は、母材(基盤材)を保護し、過酷な環境でも性能を発揮できるようになります。
ライニングは、しばしばコーティングと混同されることがありますが、両者には明確な違いがあります。
コーティングは表面に単一の膜を形成するだけであるのに対して、
ライニングは通常、数層の保護膜を積層することで、より高い耐性を発揮します。
**ピンホール(微細な穴)**ができることがあるコーティングとは異なり、
ライニングはこのような欠陥が発生しにくいのが特徴です。
特徴
・耐性の向上
ライニングは、物体に耐摩耗性、耐酸性、耐熱性、
さらには耐食性を与えるため、厳しい環境下でも使用することができます。
特に化学プラントや高温環境で使用される機器において、その重要性が際立ちます。
・複数層のコーティング
ライニングは、数層にわたるコーティングによって構成され、これが耐性を高めます。
複数層にすることで、破れやすい一層のコーティングよりも、強い保護を提供することが可能です。
・ピンホールの防止
コーティングと異なり、ライニングではピンホールが発生しにくいため、
全体的に均一で信頼性の高い保護層が形成されます。
これにより、コーティング層の耐久性や性能が長期間保たれます。
・用途に応じた選択
ライニングは使用目的に応じて材料や層数を選定する必要があります。
環境条件(湿度、酸性、温度など)に応じて最適なライニングを選ぶことが、性能を最大限に引き出すために重要です。
現場監督として重要なポイント
・適切なライニング選定
現場監督としては、ライニングの目的や用途に応じて、最適な材料や層数を選定することが必要です。
たとえば、耐熱性が求められる場所であれば、耐高温ライニングを選ぶ必要があります。
これにより、機器や設備が長期間安定して動作します。
・施工管理の重要性
ライニング施工は、複数層にわたる場合が多く、各層の乾燥時間や施工方法、厚みなどを厳密に管理することが重要です。
施工不良があれば、後の段階で不具合が発生する可能性が高まります。
・耐久性の確認
ライニングの選定や施工後には、その耐久性を確認することが必須です。
特に、過酷な使用環境に置かれる設備においては、
ライニングの効果が長期間にわたって発揮されるかどうかをチェックすることが、現場監督の役割となります。
・ライニングの劣化対策
ライニングが時間と共に劣化することもあります。
そのため、定期的な点検や再ライニングのタイミングを把握し、早期に対策を講じることが現場監督の仕事です。
劣化を放置すると、機器の故障や安全性の低下を招く可能性があります。
関連用語
・コーティング: 表面に一層の保護膜を施す処理。
ライニングと異なり、単層での処理が多い。
・耐摩耗性: 摩擦や磨耗に対しての抵抗力。
・耐酸性: 酸による腐食を防ぐ能力。
・耐熱性: 高温環境での耐久性。
・ピンホール: コーティング層にできる小さな穴。
これがあると、コーティングの保護機能が低下します。
現場管理における重要性
現場監督にとって、ライニングは設備や機器の保護と耐久性を確保するために非常に重要です。
ライニング処理が不十分だと、機器が早期に故障したり、運用コストが増大する可能性があります。
適切なライニングを選び、施工し、劣化を早期に発見して対応することは、現場監督の重要な任務の一つです。
また、ライニングの知識は、品質管理や設備の長期的な運用にも直結します。